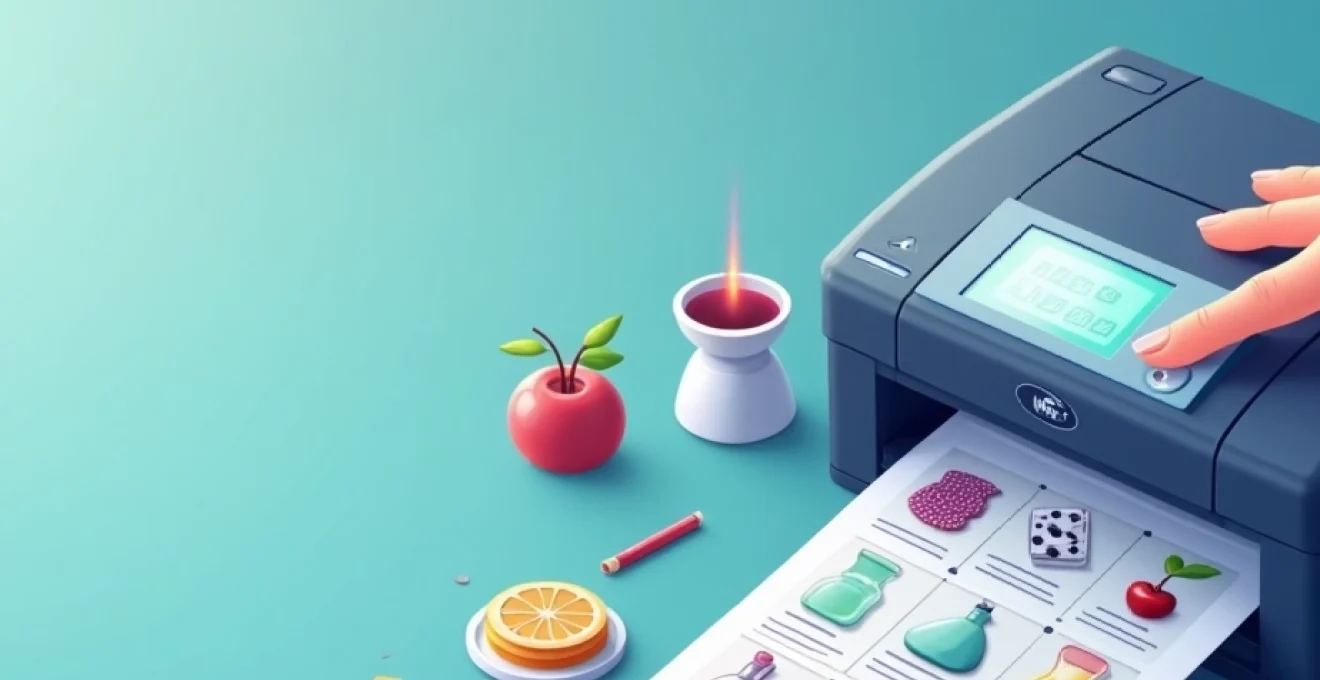
Thermal printing technology has revolutionized the world of on-demand printing, offering a fast, efficient, and cost-effective solution for producing high-quality prints. This innovative printing method utilizes heat to create crisp, clear images and text on specially designed thermal paper or labels. As businesses and industries increasingly rely on quick and reliable printing solutions, understanding the intricacies of thermal printing mechanisms becomes crucial for optimizing print quality and performance.
Thermal printing technology: core components and mechanisms
At the heart of thermal printing lies a sophisticated interplay of hardware and chemistry. The core components of a thermal printer include the thermal printhead, platen roller, and thermal media. The printhead, typically composed of a linear array of heating elements, is the primary driver of the printing process. These heating elements, also known as thermal dots, rapidly heat and cool to create the desired image on the thermal media.
The platen roller plays a crucial role in maintaining consistent contact between the printhead and the thermal media. This pressure ensures uniform heat transfer and contributes significantly to print quality. The thermal media, whether it's direct thermal paper or thermal transfer ribbons, is engineered to react to heat and produce the final image.
One of the key advantages of thermal printing is its simplicity and reliability. Unlike traditional printing methods that rely on ink or toner, thermal printers have fewer moving parts, resulting in reduced maintenance requirements and increased longevity. This makes them particularly well-suited for high-volume printing applications in retail, logistics, and healthcare industries.
Thermal printhead architecture and heat distribution
The thermal printhead is the cornerstone of the printing mechanism, responsible for translating digital information into physical marks on the thermal media. Modern thermal printheads are marvels of engineering, designed to deliver precise heat distribution for optimal print quality. Let's delve into the key aspects of printhead architecture and heat management.
Thin film resistor arrays in modern printheads
Contemporary thermal printheads utilize thin film resistor arrays to achieve high-resolution printing. These arrays consist of thousands of microscopic heating elements arranged in a linear configuration. Each element can be individually controlled, allowing for precise heat application and, consequently, intricate image reproduction. The thin film technology enables rapid heating and cooling cycles, contributing to faster print speeds and improved energy efficiency.
Pulse width modulation for precise temperature control
Pulse Width Modulation (PWM) is a sophisticated technique employed in thermal printing to achieve fine-grained temperature control. By varying the duration and intensity of electrical pulses sent to the heating elements, PWM allows for precise manipulation of heat output. This level of control is essential for producing smooth gradients and maintaining consistent print quality across different media types and environmental conditions.
Heat sink design and thermal management strategies
Effective heat management is crucial for maintaining print quality and extending the lifespan of the printhead. Advanced thermal printers incorporate sophisticated heat sink designs to dissipate excess heat quickly and efficiently. These heat sinks often feature intricate fin structures or liquid cooling systems to maximize heat transfer away from the printhead. Additionally, intelligent thermal management algorithms monitor and adjust printhead temperature in real-time, preventing overheating and ensuring optimal performance.
Ceramic substrates vs. glass substrates in printhead construction
The choice of substrate material in printhead construction significantly impacts performance and durability. Ceramic substrates have long been the industry standard, prized for their excellent thermal conductivity and resistance to wear. However, recent advancements have led to the development of glass substrates that offer comparable performance with added benefits such as improved heat distribution and reduced manufacturing costs.
When choosing a thermal printer, it is essential to consider the specific printhead technology used. High-quality printer mechanisms available from https://aps-printer.com/ often feature advanced printhead designs that optimise heat distribution and longevity, ensuring consistent print quality over long periods of use.
Thermal paper composition and chemical reactions
The magic of thermal printing lies not only in the sophisticated hardware but also in the chemistry of the thermal media. Thermal paper is engineered to react to heat, producing visible marks without the need for ink or toner. Understanding the composition and chemical reactions involved in thermal paper is crucial for appreciating the intricacies of the printing process.
Leuco dye systems: from colorless to colored states
At the core of thermal paper technology are leuco dye systems. These ingenious chemical compounds exist in a colorless state under normal conditions but undergo a remarkable transformation when exposed to heat. The thermal paper consists of multiple layers, including a base layer, a thermosensitive layer containing the leuco dyes, and a protective topcoat.
When heat is applied by the thermal printhead, it triggers a complex series of chemical reactions within the thermosensitive layer. The leuco dyes interact with developers and other compounds, resulting in a rapid color change. This process allows for the creation of sharp, high-contrast images and text. The speed and efficiency of this chemical reaction contribute to the fast printing speeds characteristic of thermal printers.
Bisphenol A (BPA) vs. BPA-free thermal paper formulations
Historically, many thermal paper formulations included Bisphenol A (BPA) as a color developer. However, concerns about the potential health and environmental impacts of BPA have led to the development of BPA-free alternatives. These new formulations utilize different chemical compounds to achieve similar color-developing properties without the associated risks of BPA exposure.
The transition to BPA-free thermal paper has been driven by regulatory pressures and increasing consumer awareness. While BPA-free options may have slightly different performance characteristics, ongoing research and development have largely bridged the gap, providing environmentally friendly solutions that maintain high print quality.
Protective coatings and their impact on print longevity
To enhance the durability and longevity of thermal prints, manufacturers apply protective coatings to the paper's surface. These coatings serve multiple purposes, including:
- Shielding the thermosensitive layer from environmental factors such as UV light and moisture
- Improving resistance to abrasion and chemicals
- Enhancing the overall appearance of the print
- Extending the lifespan of the printed image
The composition and quality of these protective coatings can significantly impact the long-term readability and durability of thermal prints. High-quality thermal papers often feature advanced coating technologies that provide superior protection against fading, smudging, and environmental degradation.
Direct thermal vs. thermal transfer printing methods
While both direct thermal and thermal transfer printing utilize heat to create images, they differ significantly in their mechanisms and applications. Understanding the distinctions between these two methods is crucial for selecting the appropriate printing solution for specific needs.
Direct thermal printing relies on heat-sensitive paper that changes color when exposed to heat from the printhead. This method is simpler and more cost-effective for short-term applications, as it doesn't require additional consumables like ribbons. However, direct thermal prints may fade over time, especially when exposed to heat or sunlight.
Thermal transfer printing, on the other hand, uses a ribbon containing ink or resin that is melted onto the printing surface by the heated printhead. This method offers greater durability and versatility, as it can print on a wide range of materials, including synthetic labels and fabrics. Thermal transfer prints are more resistant to environmental factors and are ideal for long-term applications.
The choice between direct thermal and thermal transfer printing depends on factors such as the intended lifespan of the print, environmental conditions, and the specific material being printed on.
Both methods have their place in modern printing applications, and many thermal printers are designed to accommodate both direct thermal and thermal transfer printing, offering flexibility to meet diverse printing needs.
Resolution and print quality factors in thermal printing
Achieving high-quality prints in thermal printing systems involves a complex interplay of various factors. Resolution, measured in dots per inch (DPI), is a critical metric, but it's not the only determinant of print quality. Let's explore the key elements that contribute to producing sharp, clear, and visually appealing thermal prints.
Dots per inch (DPI) and its relationship to image clarity
DPI is a fundamental measure of print resolution in thermal printing. It refers to the number of individual dots that can be placed within a linear inch. Higher DPI values generally translate to finer detail and sharper images. Common resolutions in thermal printing range from 203 DPI for basic applications to 600 DPI or higher for high-quality graphics and small text.
However, it's important to note that DPI alone doesn't tell the whole story. The size and shape of individual dots, as well as how they are arranged, also play crucial roles in determining overall image quality. Advanced thermal printheads employ sophisticated dot-shaping techniques to optimize image clarity and edge definition.
Grayscale printing techniques in thermal systems
While thermal printing is often associated with black and white output, modern systems are capable of producing grayscale images. This is achieved through a technique called dithering, where different patterns of black dots are used to create the illusion of various shades of gray.
More advanced thermal printers utilize multi-level printing technologies that can produce true grayscale images by varying the heat applied to each dot. This results in dots of different sizes or intensities, allowing for smoother gradients and more nuanced image reproduction.
Edge sharpness and the role of printhead alignment
The sharpness of printed edges is a critical factor in overall print quality, particularly for text and barcode applications. Achieving crisp edges requires precise control over heat distribution and accurate alignment of the printhead with the thermal media.
Printhead alignment is a delicate balance that must be maintained throughout the printing process. Misalignment can result in blurred edges, inconsistent print density, and poor overall image quality. Advanced thermal printers incorporate automated alignment systems and real-time adjustments to ensure optimal printhead positioning.
Thermal printing applications and industry-specific optimizations
Thermal printing technology has found widespread adoption across various industries, each with its unique requirements and challenges. Understanding these specific applications and the optimizations developed to address them provides valuable insights into the versatility and ongoing evolution of thermal printing systems.
In the retail sector, thermal printers are ubiquitous for producing receipts, price tags, and barcode labels. The demand for fast, on-demand printing in high-volume environments has driven innovations in print speed and media handling capabilities. Many retail-focused thermal printers now feature drop-in paper loading and auto-cutting mechanisms to minimize downtime during media changes.
The logistics and transportation industry relies heavily on thermal printing for shipping labels and tracking documents. Here, durability and readability under various environmental conditions are paramount. Specialized thermal media with enhanced resistance to moisture, UV light, and abrasion have been developed to meet these demanding requirements.
In healthcare settings, thermal printing plays a crucial role in patient identification, specimen labeling, and pharmacy applications. The need for absolute accuracy and compliance with strict regulations has led to the development of thermal printers with advanced error-checking features and secure printing protocols.
The adaptability of thermal printing technology to diverse industry needs underscores its importance as a versatile and reliable printing solution in modern business operations.
As thermal printing technology continues to evolve, we can expect to see further optimizations tailored to specific industry requirements. These may include advancements in mobile thermal printing for field operations, integration with IoT systems for enhanced tracking and automation, and the development of eco-friendly thermal media to address growing environmental concerns.
The ongoing refinement of thermal printing mechanisms, coupled with innovations in thermal media and software integration, ensures that this technology will remain at the forefront of on-demand printing solutions for years to come. By understanding the intricate workings of thermal printing systems and staying abreast of industry-specific developments, businesses can leverage this powerful technology to enhance their operations and meet the ever-changing demands of modern commerce.