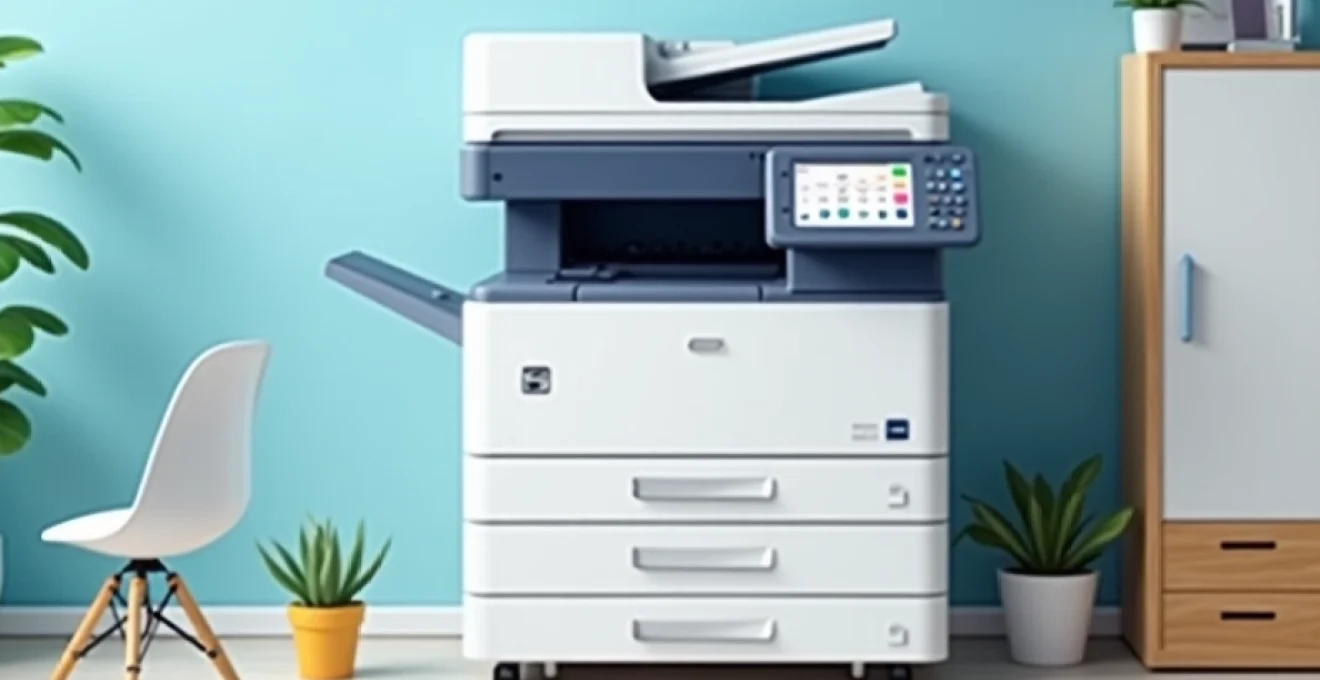
In today's competitive business landscape, every operational decision can significantly impact a company's bottom line. Selecting the right printer might seem like a minor consideration, but it can have far-reaching consequences on operational costs. The choice of printer affects not only immediate expenses but also long-term financial outcomes, productivity, and even environmental impact. Understanding the nuances of printer selection is crucial for businesses aiming to optimize their resources and maintain a lean, efficient operation.
Printers are essential tools in most office environments, but their true cost extends far beyond the initial purchase price. From energy consumption to maintenance requirements, and from consumables to output quality, each aspect of a printer's operation contributes to its overall financial impact on a business. By making an informed decision, companies can avoid the pitfalls of seemingly cheap options that may lead to inflated long-term expenses.
Total cost of ownership (TCO) analysis for printer selection
When evaluating printers, it's critical to look beyond the sticker price and consider the Total Cost of Ownership (TCO). TCO encompasses all costs associated with purchasing, operating, and maintaining a printer over its lifetime. This comprehensive approach provides a more accurate picture of the true financial impact of a printer on your business.
A thorough TCO analysis includes factors such as initial purchase price, ink or toner costs, energy consumption, paper usage, maintenance fees, and potential downtime costs. By examining these elements, businesses can make more informed decisions that align with their long-term financial goals. For example, a printer with a higher upfront cost might offer significant savings over time due to lower per-page printing costs or reduced energy consumption.
To conduct an effective TCO analysis, gather data on your current printing needs, including monthly print volumes, types of documents printed, and existing maintenance costs. Compare these figures with the specifications and projected costs of potential new printers. This comparison will reveal which options offer the best value over the printer's expected lifespan.
Print volume assessment and printer capacity matching
One of the most critical factors in selecting a cost-effective printer is accurately assessing your organization's print volume and matching it to the right printer capacity. Overestimating or underestimating your needs can lead to unnecessary expenses or insufficient productivity. A printer that's too small for your needs will wear out quickly, while an oversized printer may represent wasted capacity and higher energy costs.
Calculating pages per minute (PPM) requirements
Pages Per Minute (PPM) is a crucial metric in determining the right printer for your business. To calculate your PPM requirements, consider your peak printing periods and ensure your chosen printer can handle the load without creating bottlenecks. For instance, if your office regularly prints 1000 pages during the busiest hour of the day, you'll need a printer capable of at least 17 PPM (1000 pages รท 60 minutes).
Remember that color printing typically has a lower PPM rate than black and white. If your business frequently produces color documents, factor this into your calculations to avoid productivity slowdowns.
Duty cycle evaluation for long-term reliability
A printer's duty cycle refers to the maximum number of pages it can print per month without excessive wear. Choosing a printer with an appropriate duty cycle is essential for ensuring long-term reliability and avoiding premature breakdowns. As a rule of thumb, your average monthly print volume should not exceed 10-20% of the printer's duty cycle to maintain optimal performance and longevity.
For example, if your office prints an average of 5,000 pages per month, look for a printer with a duty cycle of at least 25,000 to 50,000 pages. This buffer allows for occasional high-volume periods without overtaxing the machine.
Paper handling capabilities and media flexibility
The right printer should be able to handle the types of media your business regularly uses. Consider factors such as paper sizes, weights, and specialized media like envelopes or labels. A printer with flexible paper handling capabilities can reduce the need for outsourcing certain print jobs, potentially saving both time and money.
Additionally, features like automatic duplexing (double-sided printing) can significantly reduce paper costs and environmental impact. Evaluate your typical print jobs and choose a printer that can efficiently handle your most common media types without frequent manual interventions.
Energy efficiency and power consumption metrics
Energy efficiency is an often-overlooked aspect of printer selection that can have a substantial impact on operational costs. Modern printers vary widely in their power consumption, and choosing an energy-efficient model can lead to significant savings over time, especially for high-volume users.
ENERGY STAR certification and ratings
Look for printers with ENERGY STAR certification, which indicates that the device meets strict energy efficiency guidelines set by the U.S. Environmental Protection Agency and the Department of Energy. ENERGY STAR certified printers typically consume 40-55% less energy than standard models, translating to lower electricity bills and reduced environmental impact.
When comparing ENERGY STAR rated printers, pay attention to the Typical Electricity Consumption (TEC) value. This metric represents the estimated kilowatt-hours used by the printer over a week, providing a standardized way to compare energy efficiency across different models.
Standby power usage and auto-off features
Standby power, also known as vampire power, can account for a significant portion of a printer's energy consumption. Look for printers with low standby power usage and features like auto-off or deep sleep modes that minimize energy use during periods of inactivity. Some advanced models can learn your office's usage patterns and automatically adjust power states for optimal efficiency.
Heat output and HVAC impact considerations
The heat generated by printers can contribute to increased cooling costs, especially in larger office environments. When selecting a printer, consider its heat output and potential impact on your HVAC system. Printers with lower heat emissions not only consume less energy but also reduce the strain on air conditioning systems, leading to additional energy savings.
Consumables cost optimization strategies
Consumables, primarily ink or toner cartridges, often represent the largest ongoing expense associated with printer ownership. Implementing strategies to optimize consumables costs can lead to substantial savings over time.
Toner yield analysis: standard vs. high-capacity cartridges
When evaluating toner costs, look beyond the price per cartridge and focus on the cost per page. High-capacity cartridges typically offer a lower cost per page compared to standard cartridges, despite their higher upfront cost. Conduct a yield analysis to determine which option provides the best value for your print volume.
For example, if a standard toner cartridge costs $50 and yields 2,000 pages, the cost per page is $0.025. In contrast, a high-capacity cartridge priced at $80 that yields 4,000 pages has a cost per page of $0.02, representing a 20% savings per page printed.
Drum unit lifespan and replacement frequency
In laser printers, the drum unit is a critical component that affects print quality and operational costs. Some printers have separate drum units, while others integrate the drum into the toner cartridge. Consider the lifespan and replacement costs of drum units when calculating long-term expenses. Printers with longer-lasting drum units or those that integrate the drum into high-yield toner cartridges can offer significant cost advantages over time.
Third-party vs. OEM supplies: quality and cost trade-offs
The decision to use Original Equipment Manufacturer (OEM) supplies or third-party alternatives can significantly impact your printing costs. While third-party supplies often come at a lower price point, they may pose risks in terms of print quality, reliability, and potential warranty issues. Carefully weigh the cost savings against these potential drawbacks, and consider conducting small-scale tests with third-party supplies before committing to their use across your organization.
Print management software integration for cost control
Implementing print management software can be a game-changer in controlling and reducing printing costs. These solutions offer a range of features designed to optimize printer usage, track expenses, and enforce printing policies across an organization.
Key features of print management software include:
- User authentication and print job tracking
- Quota management and departmental billing
- Rule-based printing to enforce duplex or black-and-white printing for certain document types
- Print job routing to the most cost-effective device
- Detailed reporting on printer usage and costs
By providing visibility into printing habits and enforcing cost-saving policies, print management software can lead to significant reductions in print volumes and associated costs. Some organizations report savings of up to 30% on their printing expenses after implementing these systems.
Maintenance requirements and service agreement evaluation
The maintenance and servicing of printers can represent a significant portion of their total cost of ownership. Understanding the maintenance requirements of different printer models and evaluating service agreement options is crucial for managing long-term costs effectively.
Preventive maintenance schedules and in-house capabilities
When selecting a printer, consider its maintenance requirements and assess your organization's ability to perform routine maintenance tasks in-house. Some printers are designed for easy user maintenance, with clear instructions for tasks like replacing fusers or transfer belts. Opting for models that allow for more in-house maintenance can reduce service calls and associated costs.
Develop a preventive maintenance schedule based on the manufacturer's recommendations and your usage patterns. Regular maintenance can prevent costly breakdowns and extend the life of your printer, ultimately reducing your total cost of ownership.
Remote diagnostics and predictive service technologies
Modern printers often come equipped with remote diagnostics capabilities, allowing service providers to monitor the device's health and predict potential issues before they cause downtime. These technologies can significantly reduce service costs and minimize disruptions to your business operations.
When evaluating printers, inquire about their remote diagnostic features and how they integrate with service provider systems. Printers with advanced predictive maintenance capabilities can offer substantial long-term cost savings by reducing the frequency and duration of service interventions.
Cost-per-page service contracts vs. time-and-materials billing
When it comes to service agreements, businesses typically have two main options: cost-per-page contracts or time-and-materials billing. Cost-per-page contracts offer predictable expenses and often include consumables, making budgeting easier. Time-and-materials billing can be more cost-effective for low-volume users but carries the risk of unexpected expenses for major repairs.
To determine the best option for your organization, analyze your historical print volumes and service needs. For high-volume users or those with critical printing needs, cost-per-page contracts often provide better value and peace of mind. However, for businesses with low print volumes or those with in-house technical expertise, time-and-materials billing might be more economical.