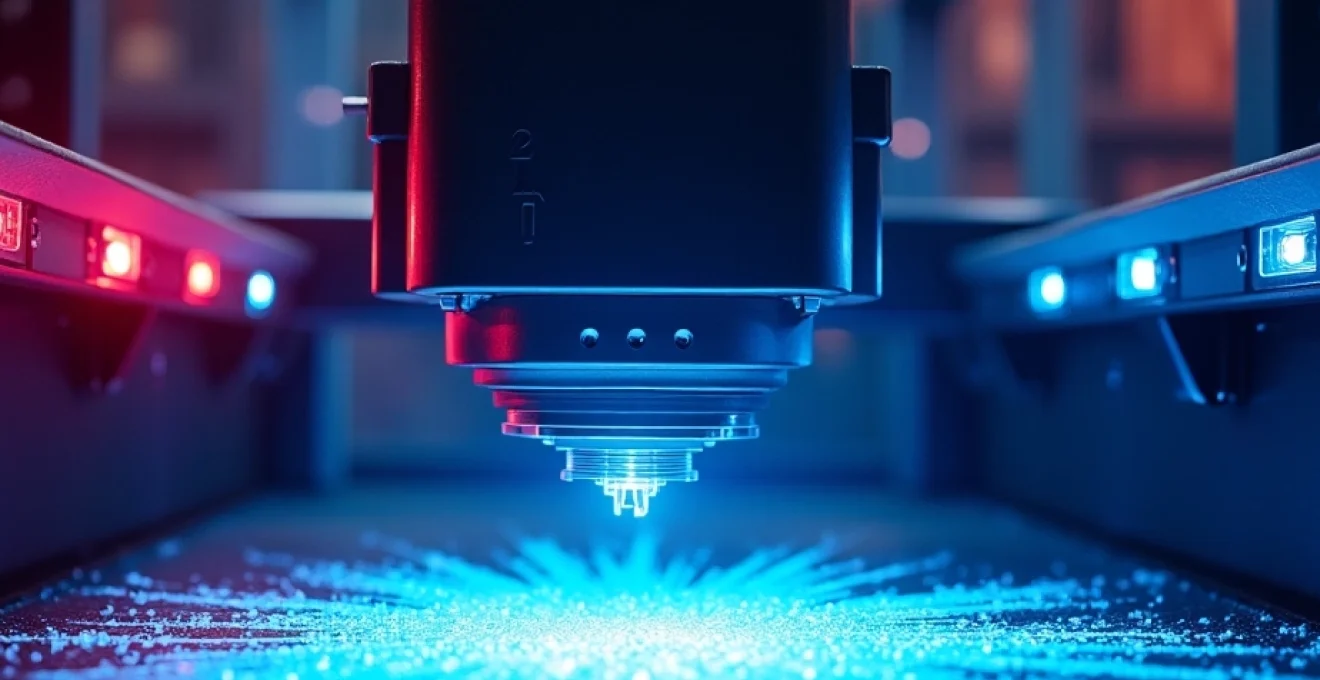
Ultraviolet (UV) printing has emerged as a transformative force in modern production, offering unprecedented speed, versatility, and quality across various industries. This innovative technology harnesses the power of UV light to instantly cure inks, revolutionizing traditional printing processes. As businesses seek more efficient, eco-friendly, and high-performance printing solutions, UV printing stands at the forefront of this technological revolution, reshaping manufacturing landscapes and opening new possibilities for customization and productivity.
UV printing technology: principles and mechanisms
At its core, UV printing relies on a photochemical process that instantly cures or dries special UV-reactive inks when exposed to ultraviolet light. This mechanism allows for rapid printing on a wide variety of substrates, including plastics, metals, glass, and even fabrics. The process begins with the application of UV-curable inks, which contain photoinitiators - chemical compounds that react to UV light exposure.
When the UV light source activates these photoinitiators, it triggers a chain reaction that causes the liquid ink to polymerize and solidify in a fraction of a second. This instant curing eliminates the need for drying time, significantly speeding up production processes. Moreover, the UV curing mechanism allows for printing on heat-sensitive materials that would be damaged by traditional heat-based drying methods.
One of the key advantages of UV printing is its ability to produce exceptionally vibrant and durable prints. The cured ink forms a tough, cross-linked polymer layer that adheres strongly to the substrate, resulting in prints that are resistant to fading, scratching, and chemical exposure. This durability makes UV-printed products ideal for both indoor and outdoor applications, from signage to packaging.
UV-LED vs. traditional UV curing systems
The evolution of UV printing technology has led to the development of two primary curing systems: traditional mercury vapor lamps and more recent UV-LED arrays. Each system has its own set of characteristics that impact performance, efficiency, and environmental considerations.
Mercury vapor lamps vs. UV-LED arrays
Traditional UV curing systems utilize mercury vapor lamps, which have been the industry standard for decades. These lamps emit a broad spectrum of UV light and generate significant heat during operation. In contrast, UV-LED arrays use light-emitting diodes to produce a more focused spectrum of UV light with minimal heat generation.
UV-LED systems offer several advantages over mercury vapor lamps:
- Instant on/off capability, eliminating warm-up and cool-down periods
- Longer operational lifespan, reducing maintenance and replacement costs
- Lower heat output, allowing for printing on heat-sensitive materials
- Compact size, enabling more flexible printer designs
However, mercury vapor lamps still maintain some advantages in certain applications, particularly where a broader UV spectrum is required for specific ink formulations.
Energy efficiency comparisons in industrial applications
When it comes to energy efficiency, UV-LED systems have a clear edge over traditional mercury vapor lamps. LED technology consumes significantly less power and converts a higher percentage of electrical energy into usable UV light. In industrial settings, this translates to lower operational costs and reduced environmental impact.
A comparative study of energy consumption in large-scale printing operations revealed that UV-LED curing systems can achieve energy savings of up to 70% compared to mercury vapor systems. This substantial reduction in energy use not only lowers production costs but also aligns with the growing emphasis on sustainable manufacturing practices.
Spectral output and ink compatibility analysis
The spectral output of UV curing systems plays a crucial role in ink compatibility and curing efficiency. Mercury vapor lamps produce a broad spectrum of UV light, which can effectively cure a wide range of ink formulations. UV-LED arrays, on the other hand, emit a narrower spectrum of light, typically centered around specific wavelengths such as 365nm, 385nm, or 395nm.
This spectral difference has implications for ink formulation and compatibility. While many modern UV inks are designed to work with both mercury vapor and LED systems, some specialized applications may require specific spectral outputs for optimal curing. As UV-LED technology continues to advance, the development of new photoinitiators and ink formulations is expanding the range of LED-compatible inks, further driving the adoption of this more efficient curing technology.
Advanced materials in UV printing
The rapid advancement of UV printing technology has been accompanied by significant innovations in materials science, particularly in the development of UV-curable inks and compatible substrates. These advancements have expanded the applications of UV printing and enhanced the quality and durability of printed products.
Photoinitiators and their role in UV-curable inks
Photoinitiators are the cornerstone of UV-curable ink technology. These specialized chemical compounds absorb UV light and generate reactive species that initiate the polymerization process. The choice of photoinitiator significantly influences the curing speed, depth of cure, and final properties of the printed material.
Recent developments in photoinitiator technology have led to the creation of highly efficient compounds that can cure inks faster and with lower energy input. For instance, the introduction of Type II photoinitiators
has enabled curing under low-intensity UV-LED light, further improving energy efficiency and expanding the range of printable substrates.
Substrate compatibility: from plastics to metals
One of the most significant advantages of UV printing is its ability to adhere to a wide range of substrates. This versatility has revolutionized product decoration and industrial printing processes across multiple sectors. Modern UV inks can bond effectively to:
- Various plastics, including PET, PVC, and polycarbonate
- Metals, such as aluminum, steel, and copper
- Glass and ceramics
- Wood and composite materials
- Textiles and synthetic fabrics
The development of specialized primers and adhesion promoters has further expanded the range of compatible substrates, allowing UV printing on previously challenging materials like certain silicone-based products.
Nanoparticle-enhanced UV inks for enhanced properties
The integration of nanotechnology into UV ink formulations has opened up new possibilities for enhancing print quality and functionality. Nanoparticle-enhanced UV inks offer several advantages:
Improved durability and scratch resistance : By incorporating nanoparticles such as silica or alumina, UV inks can achieve significantly higher abrasion resistance, making them ideal for high-wear applications like flooring or automotive parts.
Enhanced color vibrancy and opacity : Nanoparticles can increase the refractive index of inks, resulting in more vibrant colors and improved opacity, especially in white and metallic inks.
Functional properties : The addition of specific nanoparticles can impart unique properties to printed surfaces, such as antimicrobial activity, conductivity, or heat resistance.
The marriage of nanotechnology and UV-curable inks represents a quantum leap in printing capabilities, enabling us to create surfaces with properties that were previously unattainable through conventional printing methods.
UV printing in industry 4.0 manufacturing
As manufacturing enters the era of Industry 4.0, UV printing technology is evolving to integrate seamlessly with smart factory systems and Internet of Things (IoT) networks. This integration is driving unprecedented levels of automation, quality control, and production efficiency.
Integration with IoT and smart factory systems
UV printing systems are increasingly being equipped with IoT-enabled sensors and communication modules, allowing them to become integral parts of smart manufacturing ecosystems. This connectivity enables real-time monitoring of printing parameters, remote diagnostics, and automated workflow optimization.
In a smart factory setting, UV printers can communicate with other production equipment, inventory management systems, and enterprise resource planning (ERP) software. This interconnectedness facilitates:
- Just-in-time production scheduling
- Automated material handling and replenishment
- Seamless integration with digital workflow management
- Enhanced traceability and quality assurance
Real-time quality control through UV sensor networks
Advanced UV printing systems now incorporate sophisticated sensor networks that monitor critical parameters in real-time. These sensors can track factors such as UV intensity, ink viscosity, curing temperature, and substrate characteristics. By continuously analyzing this data, the system can make immediate adjustments to ensure consistent print quality.
For example, if a sensor detects a slight decrease in UV lamp output, the system can automatically increase lamp power or slow down the printing speed to maintain optimal curing. This real-time quality control significantly reduces waste and improves overall product consistency.
Predictive maintenance for UV printing equipment
The integration of IoT technology in UV printing systems enables predictive maintenance strategies that can dramatically reduce downtime and extend equipment lifespan. By analyzing data from various sensors, machine learning algorithms can predict potential failures before they occur.
Predictive maintenance in UV printing might include:
- Monitoring UV lamp performance to schedule replacements before output degrades
- Tracking printhead nozzle health to prevent clogging and maintain print quality
- Analyzing ink consumption patterns to optimize supply chain management
- Monitoring mechanical components for signs of wear to schedule timely maintenance
This proactive approach to maintenance not only reduces unexpected downtime but also optimizes the performance and longevity of UV printing equipment.
Environmental impact and sustainability of UV printing
As industries worldwide prioritize sustainability, UV printing has emerged as a more environmentally friendly alternative to traditional printing methods. Its reduced environmental impact stems from several key factors, including lower emissions, energy efficiency, and material conservation.
VOC emissions reduction compared to solvent-based printing
One of the most significant environmental advantages of UV printing is the dramatic reduction in volatile organic compound (VOC) emissions. Unlike solvent-based inks that release harmful VOCs during drying, UV-curable inks contain little to no VOCs and cure instantly upon exposure to UV light.
A comparative study of printing technologies revealed that UV printing can reduce VOC emissions by up to 98% compared to traditional solvent-based methods. This reduction not only improves air quality in printing facilities but also contributes to overall environmental protection by minimizing the release of ozone-depleting substances.
Energy consumption analysis: UV vs. conventional drying methods
UV printing's energy efficiency is another key factor in its environmental profile. The instant curing process eliminates the need for energy-intensive drying ovens or lengthy air-drying periods. This results in significant energy savings, particularly in high-volume production environments.
A comprehensive energy consumption analysis comparing UV printing to conventional heat-based drying methods yielded the following results:
Printing Method | Energy Consumption (kWh/1000 m²) | CO2 Emissions (kg/1000 m²) |
---|---|---|
UV-LED Printing | 15-25 | 7-12 |
Traditional UV Printing | 30-50 | 14-24 |
Solvent-Based Printing | 80-120 | 38-57 |
These figures demonstrate the substantial energy and emissions reductions achievable through UV printing, particularly with the adoption of UV-LED technology.
Lifecycle assessment of UV-Curable materials
To fully understand the environmental impact of UV printing, it's essential to consider the entire lifecycle of UV-curable materials, from production to disposal. Lifecycle assessments (LCAs) of UV-curable inks and coatings have revealed several environmental benefits:
Reduced raw material consumption : UV-curable materials typically have a higher solids content than solvent-based alternatives, resulting in less material waste and more efficient use of resources.
Longer product lifespan : The durability of UV-cured prints often leads to longer-lasting products, reducing the need for frequent reprints or replacements.
Recyclability : Many UV-cured products can be recycled more easily than those produced with solvent-based inks, as they don't contaminate the substrate with residual solvents.
The shift towards UV-curable materials represents a significant step in reducing the printing industry's environmental footprint, aligning with global sustainability goals and consumer demand for eco-friendly products.
Future trends and innovations in UV printing technology
The field of UV printing continues to evolve rapidly, with ongoing research and development promising exciting advancements in the near future. These innovations are set to further enhance the capabilities, efficiency, and applications of UV printing technology.
Advancements in UV-LED curing for High-Speed production
The push for faster production speeds in UV printing is driving significant advancements in UV-LED technology. Next-generation UV-LED systems are being developed with higher power outputs and more efficient cooling mechanisms, enabling faster curing speeds without compromising print quality.
Researchers are also exploring the potential of multi-wavelength LED arrays
that can emit different UV spectra simultaneously. This innovation could allow for more precise control over the curing process, optimizing it for different ink formulations and substrate types.
3D UV printing: emerging applications and challenges
The convergence of UV printing and 3D printing technologies is opening up new possibilities for creating complex, multi-material objects with functional properties. UV-curable resins are already widely used in stereolithography (SLA) 3D printing, but emerging technologies are pushing the boundaries further:
- Multi-material 3D UV printing for creating objects with varying material properties
- High-resolution UV printing for producing detailed microstructures and optical components
- Continuous liquid interface production (CLIP) using UV curing for ultra-fast 3D printing
While these advancements offer exciting possibilities, they also present challenges in terms of material development, process control, and scaling for industrial applications.
Biotechnology-inspired UV-Curable materials
The intersection of biotechnology and UV printing is yielding innovative materials with unique properties and environmental benefits. Researchers are exploring bio-based monomers and oligomers derived from renewable resources as alternatives to petroleum-based UV-curable materials.
Some promising developments in this area include:
Biodegradable UV-curable resins : These materials can break down naturally after their useful life, reducing environmental impact.
Bio-mimetic UV-curable coatings : Inspired by natural structures, these coatings can impart properties like self-cleaning or water repellency to printed surfaces.
UV-curable hydrogels : These materials have potential applications in biomedical printing, such as creating custom implants or tissue scaffolds.